3D Printing is a process of layering a plastic-like polymer over one another to create three-dimensional objects. Most printers work differently, but generally, the same principles apply.
Industrial printing solutions allow businesses to produce parts closer to the point of need, reducing freight costs and environmental impact. They also enable companies to use specialized materials with complex lattice structures. Click Here to learn more.
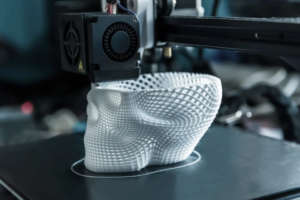
- Rapid Prototyping
3D Printing elevates a design from virtual to physical, enabling designers to iterate on concepts and see how their ideas look and feel in real life. This can result in better designs that improve functionality and user experience while decreasing manufacturing costs. In addition, physical models allow teams to perform various tests that cannot be replicated with a computer simulation. This allows for a more thorough product quality and performance evaluation, reducing risk and improving safety.
To get started, a digital 3D model is created using CAD software such as Solidworks, Autodesk Fusion, Onshape, ANSYS or many other options. The resulting file is then exported as an STL, the universal input file format for industrial 3D printers. From there, users simply hit print, and the prototype is ready to be tested or evaluated within hours.
With the right technology, the speed at which prototypes can be produced can be accelerated even further. For instance, some industrial 3D printers have the ability to produce a prototype and build the tooling or final part all on the same platform. This eliminates the need for adjustments to accommodate limitations of traditional subtractive manufacturing, and enables a more seamless transition to production.
The roots of rapid prototyping with 3D Printing go back to traditional fabrication techniques like topography and photosculpture, which used layers of hardening photographic polymer resin to create a casting mold. Today, the rapid prototyping process with 3D Printing has grown exponentially in sophistication and capability. The technology has been hailed as the fastest and most cost-effective way to bring new products to market. This has inspired a groundswell of adoption by companies across industries, with no signs of slowing down.
- Versatility
The ability to 3D print in a variety of materials provides a versatile solution that can be adapted to suit nearly any production need. It can be used for prototyping, tooling, end-use parts, or any application where a traditional model or mould would normally be required. It eliminates the upfront cost of creating molds or establishing a production line, which significantly lowers costs for smaller run productions and prototypes.
For product developers and engineers, 3D Printing opens up a world of possibilities. With the flexibility to iterate prototypes rapidly and inexpensively, they can create design changes without reworking complex mechanical components, thereby reducing overall development time and eliminating expensive retooling. This brisk pace of product development also encourages innovation, allowing designers and engineers to explore realms previously considered unreachable.
A growing number of consumer products are being 3D printed, including eyewear, jewelry and clothing. Even metals are being 3D printed, bringing a revolutionary capability to manufacturing metal products that were previously impossible to fabricate without expensive and time-consuming machining. This allows manufacturers to make a larger range of products, reduce unit cost and shorten the lead time for new product launches.
Beyond consumer products, many businesses are utilising 3D Printing for a wide variety of applications that require advanced manufacturing capabilities. This includes rapid prototyping for the medical industry, with 3D printed prosthetics and surgical tools. GE aviation, for example, is using 3D-printed Cobalt Chrome fuel nozzles that weigh 25 percent less and are five times stronger than those of traditionally manufactured nozzles. They also allow for more flexibility in fueling and handling, which is especially important in flight conditions where safety is paramount.
- Strength & Weight
While 3D Printing is often associated with toys and hobbyist items, it can also produce parts that are functional prototypes or end-user components. In fact, a lot of companies in the automotive, aerospace and energy industries have integrated the technology into their production processes. This allows them to manufacture complex parts quickly and reduce the time needed for design iterations. The technology also provides the ability to create custom parts, enabling them to meet specific requirements such as weight and strength.
The strength of a printed part depends on many factors including the geometry/shape of the model, the printer and slicer settings and the material used. Choosing a plastic with high strength and resilience is key for this type of application, such as ABS, PLA or polycarbonate. In addition to the plastic, the type and percentage of infill will determine the strength of the part.
It’s important to note that the tensile strength of a printed part is much stronger along the XY-axis than it is on the Z-axis, especially for tall and thin prints. Orienting the part correctly can significantly increase the strength of the part.
Another factor is the post processing of the print. Unskilful sanding, cutting or filing can cause the material to weaken and break. In addition, overly quick cooling can affect adhesion of layers and reduce the strength of the printed part.
In order to achieve the best strength for a particular part, it is advisable to contact a 3D printing expert as they will be able to recommend the right material and optimize the print for its desired application. This can include shape optimisation, topology optimisation, AI-based optimisation and simulation capabilities.
- Environmentally Friendly
With an increasing number of consumers and businesses prioritizing environmentally conscious practices, 3D Printing offers a solution. The use of this manufacturing technology significantly reduces carbon emissions and waste. Not only does it minimize the need for large manufacturing facilities, but it also eliminates energy waste caused by storing products and materials. Moreover, on-demand 3D Printing allows for production to take place close to home, further decreasing environmental impact by avoiding transportation.
While traditional fabrication processes result in substantial material waste, 3D Printing eliminates this problem. Fused deposition modeling (FDM) 3D printers only use the exact amount of filament needed to produce an object, eliminating excess materials. This allows for greater design flexibility and a reduced carbon footprint.
Additionally, the use of renewable materials like cellulose and plant-based plastics helps to mitigate pollution. These alternatives are far more eco-friendly than conventional petroleum-based plastics, which contribute to the Great Pacific garbage patch and can contaminate water sources, harming marine life and impacting human health.
3D Printing also enables the use of recycled materials, which can greatly decrease overall environmental impacts. Currently, most 3D printers use a combination of thermoset and thermoplastic materials. Thermosets harden when cured, while thermoplastics melt upon heating. The latter is more recyclable as it can be melted and reshaped without breaking down chemical bonds.
Furthermore, since most 3D printers are small in size, they can be used to produce products and prototypes on-demand. Compared to traditional shipping methods, which consume a lot of energy, this can greatly reduce the amount of harmful greenhouse gasses and air pollutants released. Moreover, if produced close to homes, 3D printed products also lower the risk of damage during transit and thereby reduce the need for costly repairs.
- Fast Time-to-Market
The time to market is the key for a successful product launch. In contrast to traditional manufacturing processes that rely on external sourcing, 3D Printing can dramatically cut the process. This helps businesses reclaim control over production and slash costs, speeding up development times by up to 50%. With the 3DEXPERIENCE Marketplace Make platform by Dassault Systemes, it’s easy to find service providers and manufacturers that offer certified parts based on the technology and finish you’re looking for. The platform also groups dozens of technologies, materials, finishes, certifications and lead times to provide you with instant quotes based on your design.
The 3D printer industry is a multi-billion dollar market that’s driven by a range of players, from the printer manufacturers themselves to CAD suites and slicers, which prepare files for Printing. There are a wide variety of 3D printing materials, too, ranging from the standard thermoplastics like ABS and PLA to metals that can be printed using Directed Energy Deposition (DEM), which uses a nozzle to apply a metal powder to the surface while an energy source melts it.
3D Printing also offers the ability to create cheap tooling for end-use parts, which reduces manufacturing costs and allows designers to iterate quickly and test different designs. This is particularly important for industries that are highly competitive and need to be able to respond to market forces quickly.
For example, dentists have no way of forecasting what kinds of cases they’ll see in any given week, so 3D Printing lets them produce a wide variety of custom products for their patients, such as surgical guides, night guards and crowns. This allows them to build trust, reputation and referrals while boosting revenue. The same principles can be applied to manufacturers and large production companies, allowing them to flex their production capabilities on demand and boost supply chain resilience.