Sealcoating gives faded asphalt pavement a new, smooth look and provides a protective coating that resists water, sun and oil. It increases your property value and improves curb appeal.
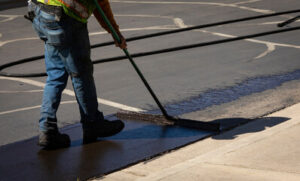
Professional pavement contractors use robust cleaning equipment such as blowers and rotary brooms, and they will repair any cracks in the paved surface prior to applying the sealcoat. They can apply the sealcoat by spray or squeegee. Visit https://www.rochesternysealcoating.com/ to learn more.
In order for sealcoating to work properly, the surface it’s being applied to must be in good condition. That means that all cracks should be filled, potholes patched, and severely damaged areas replaced if necessary. In addition, the asphalt must be dry before starting work. Once that’s done, the area should be closed off to pedestrians and vehicular traffic using barricades and possibly warning tape. Sprinklers should also be turned off so that the area doesn’t get wet before and during the application process.
Before beginning the sealing process, the pavement should be thoroughly cleaned using a pressure washer. This helps to ensure that the new coat will adhere well to the blacktop. It’s important to remove all dirt, loose pebbles, paint chips, and other debris from the pavement. Additionally, any oil or gasoline stains should be flash heated before they can be sealed over. This prevents the petroleum stains from interfering with the bond between the old and new coatings.
Next, the area should be swept clean and all weeds pulled. It’s a good idea to do this a few days before the day of the sealcoat application, as the driveway or parking lot will need time to dry completely. This will help to make sure that the finished product looks its best and isn’t marred by any unsightly weeds or oil spots.
Lastly, the area should be graded and leveled to make sure that the asphalt is as even as possible. If the pavement isn’t level, it could lead to a number of problems, including uneven wear, skids, and general poor performance.
The most critical step is to pick a few days of dry weather for applying the sealcoat. It’s impossible for the asphalt to properly cure if it gets wet before and afterward. Additionally, the temperature must be above 50 degrees in order for the sealcoat to set properly.
Before starting the actual sealing process, it’s a good idea to give all employees who will be working on the project a brief training session on how to handle the equipment safely. Coal tar emulsions and other sealcoat materials contain a large amount of chemicals that are dangerous for people to handle. It’s also essential to keep everyone away from the area until the asphalt is fully cured and dried.
Mixing
Sealcoating is a preventative maintenance treatment for asphalt pavement, and it is extremely effective when TIMED PROPERLY. Proper preparation of the surface, crack filling if needed, and application of coal tar based pavement sealer under ideal weather conditions is the key to success. In addition, proper use of a professional grade asphalt equipment such as squeegees, brushes or sprayers is also critical.
Before any work begins, the asphalt must be thoroughly cleaned to ensure that a good bond is established with the new coating. A professional asphalt contractor will use powerful cleaning equipment such as blowers and rotary brooms to remove dirt, debris, grease and oil spills, paint and other markings that were used on the parking lot for line striping and delineation of parking spaces.
The next step is mixing the sealcoating materials. The most important thing to remember is that these materials are toxic and must be handled properly in order to protect the health of those who work with them. Workers should wear masks, eye protection and rubber gloves when working with these chemicals. One instance of contact probably won’t hurt, but repeated exposure can lead to cancer and other serious medical problems.
Most pavement sealers are supplied as concentrates (undiluted) that must be mixed with water, silica sand and additives for proper application consistency according to the manufacturer’s recommended mix design. The use of clean, potable water that is low in hardness and iron will help produce an even cure and avoid streaking.
There are many different types of sand that can be used to make up the mix design for a sealer. Boiler slag is sometimes used, but many sealer producers prefer to use clean, quartz angular, silica sand because it has better surface absorptivity and becomes an integral part of the cured coating, whereas boiler slag can flake off the cured coating. The sand must be dry and free of contaminants such as clays, limestone and other aggregates. It is also important that the sand is graded to be consistent in size in order to achieve a uniform appearance when applied to the pavement surface.
Applying
Seal coating is an effective way to protect your asphalt investment. It also helps restore the black, shiny appearance of freshly-laid pavement. It forms a protective barrier against UV rays, water, oil and other oxidizing substances that can degrade your asphalt. It strengthens your asphalt by replenishing the degraded petroleum binder and specially formulated oils. It also increases surface friction to help prevent tire skidding, which causes pavement damage and safety hazards.
Before sealcoating, your asphalt needs to be clean. During the preparation process, your professional pavement contractor will blow out all lines of cracks with air blowers and sweep away any dirt and debris. They will also use a pressure sprayer to remove any oil and gas spills that may be present. Once the pavement is cleaned, it will be prepped for sealcoating by removing any weeds or other vegetation that are growing within the cracks of your pavement. This is important because the sealcoat will not adhere to weeds or dirt.
Once the area is prepped, your professional pavement contractor will begin applying the first coat of sealer. The sealer is applied to the paved surface using state-of-the-art equipment. For large areas, this will be done with a ride-on sealcoat application rig, while smaller areas can be sealed with either a squeegee or thick nap roller. During the application process, your pavement contractor will be mindful to avoid any overspray on sidewalks, curbs or buildings. All roadway ends are brushed by hand to reduce the possibility of any overspray on them as well.
There are different types of sealcoats available, including coal tar, asphalt emulsion, oil-based and fast-dry. Coal tar is a natural product that has been refined to produce a high-quality, durable material that can last up to five years. It is the favored type of sealcoat because it provides the best protection against water and UV rays while also being non-polluting. Asphalt emulsions are water-based and are not as dense or as long-lasting as coal tar. They can be used in small areas as a temporary fix until the coal tar can be re-applied.
Drying
Sealcoating is not a quick process, and it’s important to let the material dry before driving or other activities take place. It takes the surface about 36 to 48 hours for the coating to reach full strength. Humidity is a big factor that affects the speed at which it dries. Humidity slows down the drying process by preventing the water from leaving the coating as it evaporates. Ideally, humidity should be below 60 percent for the fastest drying time.
The type of sealcoat you use can also impact the curing process. Coal tar sealcoats typically take longer to dry than other types of sealcoating, because they are petroleum-based. However, this type of coating provides excellent protection and is resistant to both water and UV rays.
Other types of sealcoating are non-petroleum based, and they can take longer to dry as well. They can be used on any asphalt pavement and offer good performance. However, these products may not be as durable and may require reapplication more frequently than coal tar-based sealcoats.
When working with these chemicals, workers must wear long sleeved shirts, pants and impervious boots, as well as face masks. The toxins in these materials are carcinogenic, and repeated exposure can lead to health issues. They can also cause skin or lung irritation in sensitive individuals. It’s always wise to read the manufacturer’s material safety data sheets before using them.
Choosing the right location to apply the sealcoat is also important. Typically, the application should take place in sunny weather with temperatures above 50 degrees Fahrenheit. The area should be free of debris, and any cracks that have not been filled need to be repaired first.
In addition to extending the life of the asphalt, sealcoating can also improve the appearance of a commercial parking lot. In most cases, two coats of the product are recommended for the best results. However, it is possible to get a nice look with one coat, but it will likely not have the hardness that comes from proper curing and could allow for tracking of sand or dirt onto shoes or vehicle tires.